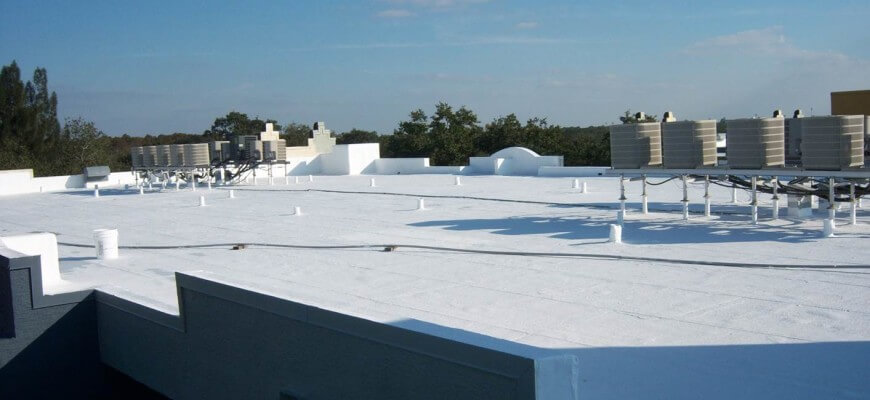
Benefits of Roof Restoration over BUR Cap Sheet
Did you know that the average commercial built-up roof (BUR) will require repairs by its 8th birthday?
Built-up asphalt with granulated cap sheet is a common traditional roofing system used for low-sloped and flat roof designs. Most commercial and industrial type buildings are designed with a low-sloped or flat roof. A BUR has a life expectancy of 15-20 years with repairs to ponds, curbs, drains and penetrations starting early in the life cycle.
The truth is that BUR systems will require maintenance repairs in the ponding areas and at seams and penetrations throughout its lifespan to keep the roof from leaking. Leaks found in low-sloped and flat roofs are most commonly caused by ponding water and thermal cycling from sun exposure. Even when installed to specification with proper maintenance, a BUR does not have coverage for leaks in ponding areas.
Thermal cycling and water, especially ponding water, erode the mineral cap of BUR leaving the black asphalt exposed. Asphalt is not UV resistant and absorbs heat and UV radiation.
Once the granulated surface has worn off of a traditional BUR, often white acrylic roof coatings are used as maintenance to protect the asphalt from further UV deterioration. Acrylic roof coatings will add UV resistance to the exposed asphalt but will not protect against water intrusion, especially a roof with ponding water.
By investing in a roof restoration system over a BUR you can eliminate the need for future roof replacement. Roof restoration systems are monolithic and don’t usually require that business operations be interrupted during installation. Roof restorations are less expensive than roof replacement and offer a tax benefit as a maintenance expense.
What happens to a BUR that is not properly maintained?
The heat and UV cause the asphalt sheet to dry out and crack. At this point the roofing material can no longer move with thermal cycles and the seams separate. Once the exposed fiberglass mat and felt become dried out, deterioration of the BUR system accelerates. By this time, the mastic around penetrations has also become brittle and split allowing for water intrusion into the BUR system and leaks appear inside the building.
If a BUR is already showing signs of leaks, an acrylic roof coating is not the solution. It is usually at this point in the lifespan of a BUR that a roof restoration is recommended to prevent saturated insulation, plywood or metal substrate damage and mold.
When considering a roof restoration system, ask for proof on the roof! For nearly 20 years, Field Testing has proven that restoring an existing traditional roof system with a SureCoat Roof Restoration System lowers the cost of roof maintenance, roof repairs and future roof budgets. Additional Field Testing proves that a SureCoat Roof Restoration System will not leak under Ponding Water.
Facts and Benefits of a SureCoat Roof Restoration:
- Ponding water will not void the roof warranty
- Cool Roof Compliant for the life of the system
- Energy savings of up to 30%
- Waterproof epoxy-hybrid; Not an acrylic
- Renewable every 10 or 20 years
- Resistant to animal fats, mold, mildew and most chemicals
- Excellent adhesion to existing roofing materials
- No penetrations in the roof deck
- Self-Adhered, Self-Flashing and Self-Priming; No separate flashings or primers
- Easy to install
- Cost less than roof replacement
- No tear-off required; Installed over existing roof system
- Tax savings as a maintenance cost
- Non-disruptive to tenants
- HVAC units do not need to be shut down
- Low VOC; No offensive odors
Not all roof restorations are the same. Be Sure with SureCoat. Call 877-823-7873 for a FREE Quote today.